At Whiteley, our legacy of crafting exceptional scissors dates back to 1760. Each pair of scissors is meticulously handcrafted in Sheffield, England, reflecting centuries of expertise and dedication.
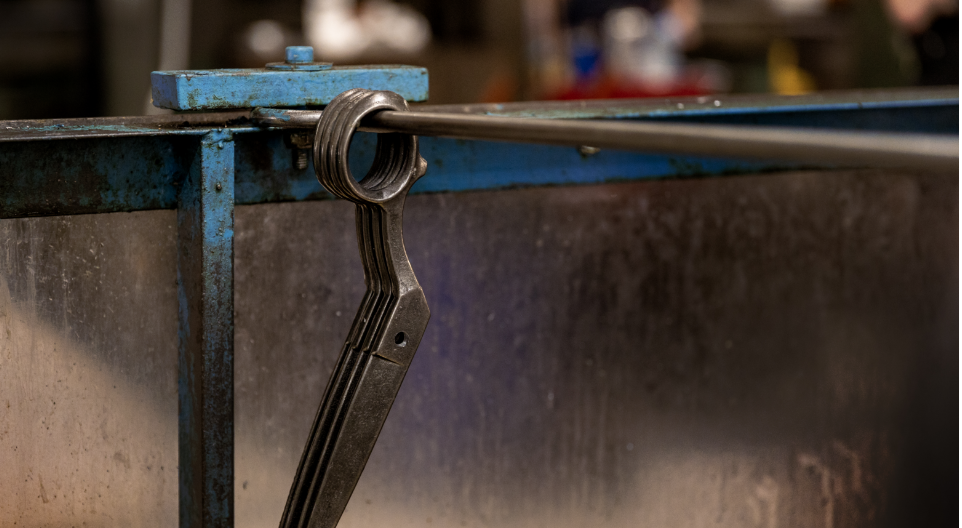
01
Forging & Trimming the Blanks
Our process begins with drop forging, where individual scissor halves, known as ‘blanks,’ are stamped from premium carbon steel bars. Each scissor style has its own unique mould, ensuring precision and consistency. The forged blanks then undergo trimming to remove excess steel and shape the insides of the handles. These raw pieces are then sent to our factory, where skilled craftsmen transform them into scissors that are as comfortable to hold as they are capable of maintaining a sharp edge.
02
Bow Dressing
-
The process of bow dressing removes roughness from the blanks. Every surface, including the delicate insides of the handles, is carefully sanded down by hand, ensuring a flawless finish and a smooth, comfortable grip.
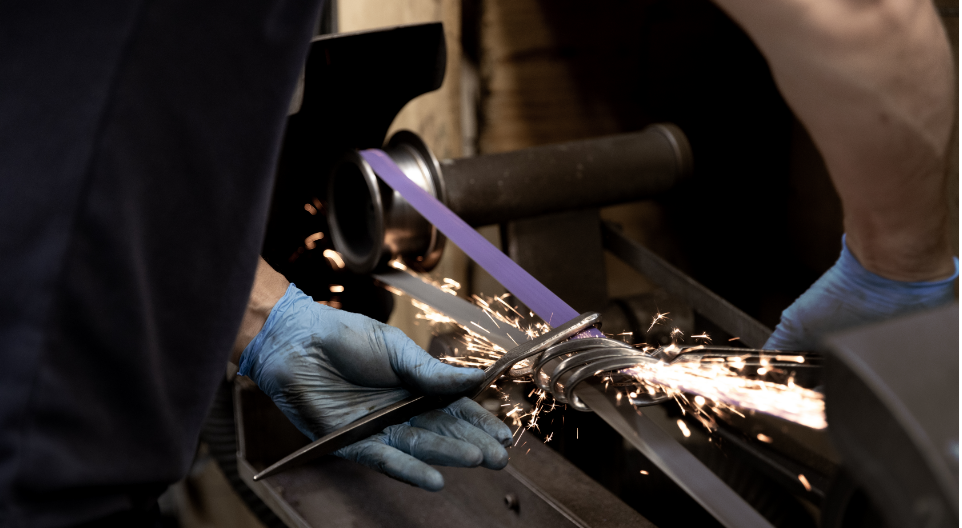
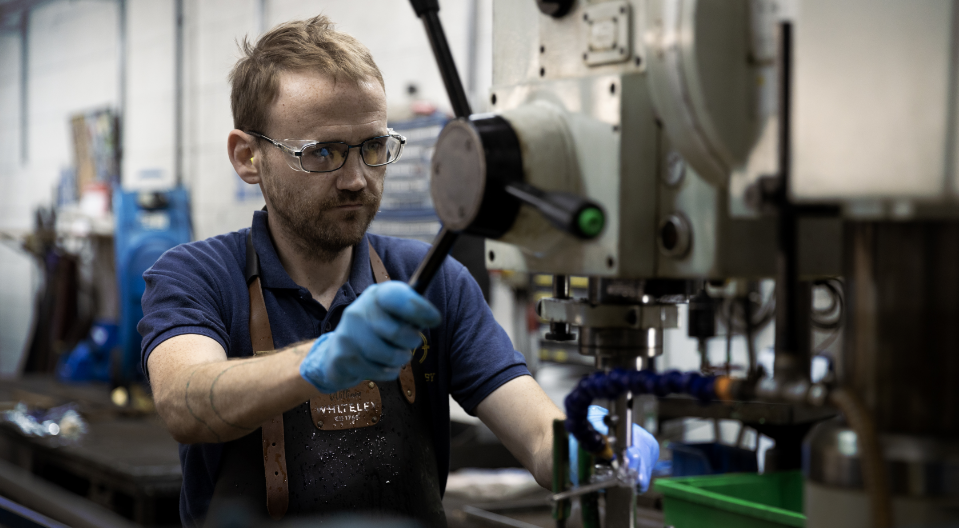
03
Drilling and Tapping
Each pair is accurately drilled and tapped where the pivot screw is inserted. This ensures optimal alignment and functionality of the finished scissor.
04
Hardening and Tempering
To achieve the necessary hardness for a durable cutting edge, the blanks are heated in a furnace and then quenched in oil. This hardening is followed by a tempering process to ensure the handles are malleable enough to be worked.
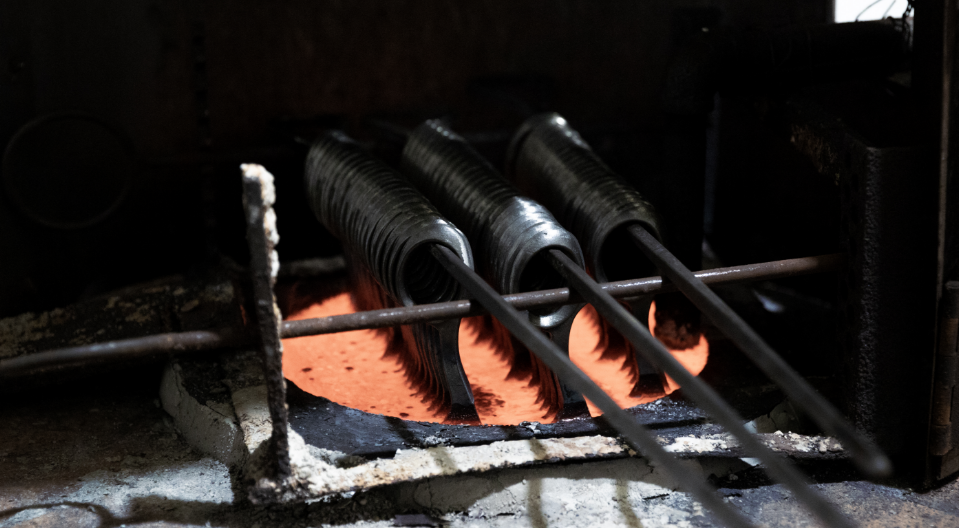
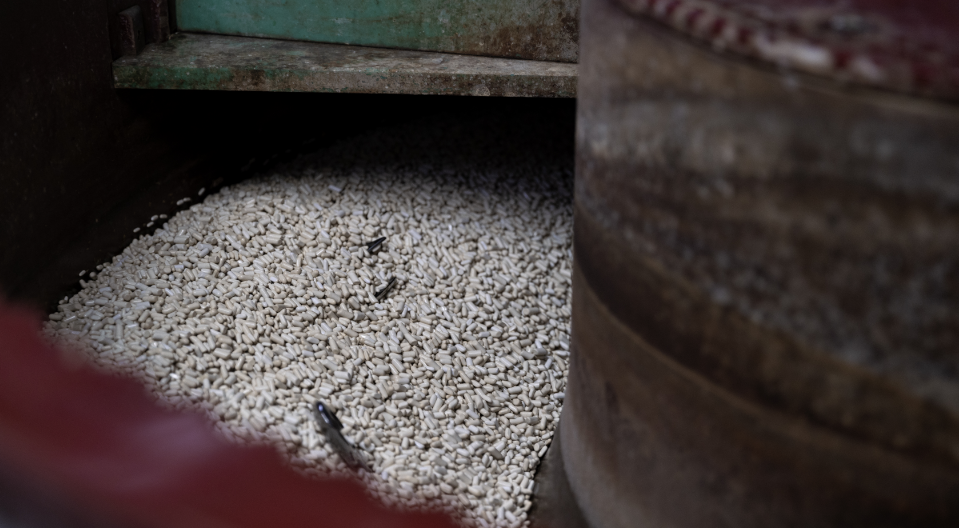
05
Rumbling and Polishing
Today, we use a vibratory rumbler filled with ceramic chips and a mild acid to smooth the rough surfaces. The constant motion gently polishes the scissors. After this, each pair is hand-polished to give them their brilliant, lasting sparkle.
06
Grinding and Sharpening
Our artisans then grind the blades to create precise, sharp edges. This meticulous process ensures each pair of scissors delivers exceptional cutting performance, meeting the high standards synonymous with the Whiteley name.
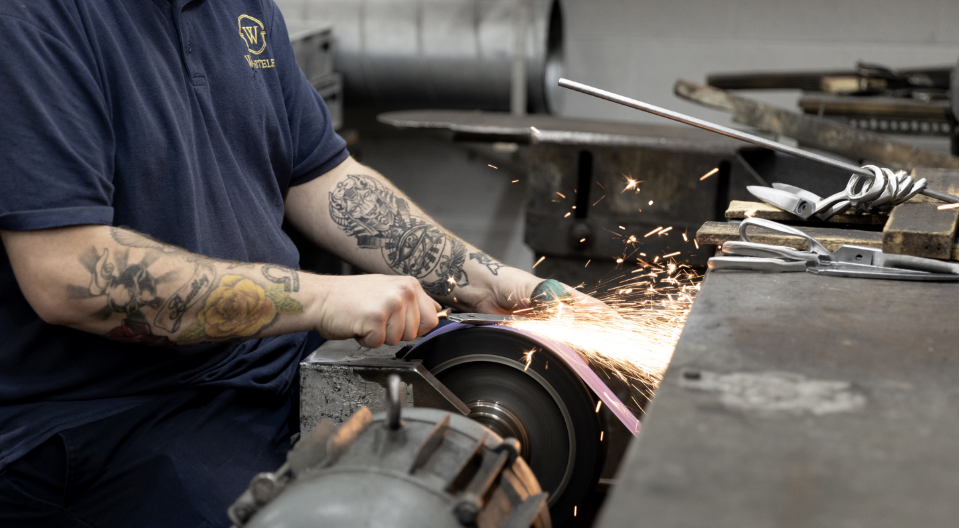
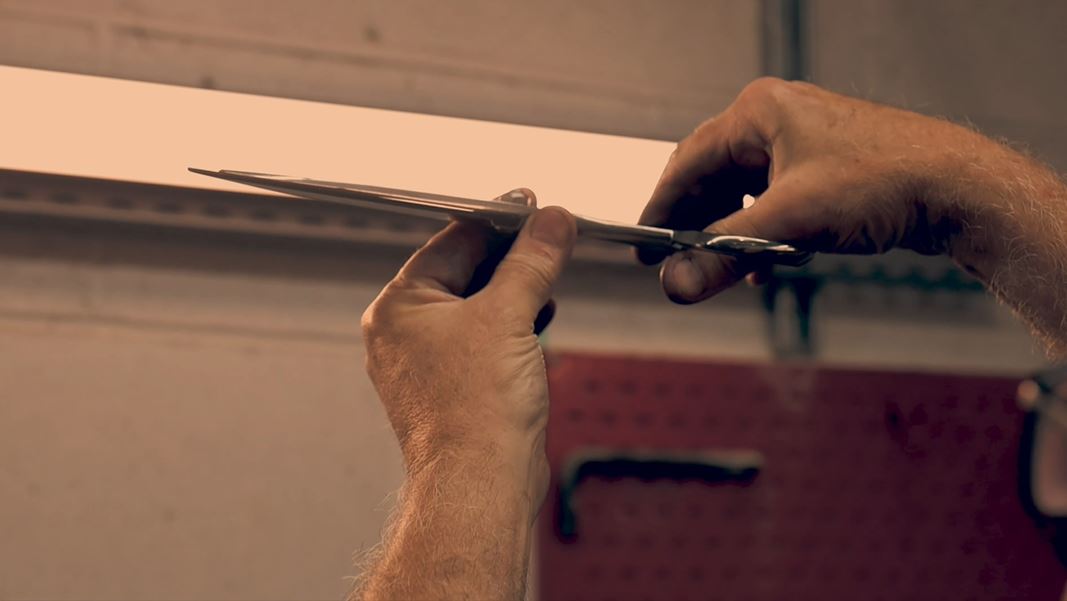
07
Final Assembly
Finally, the blades are carefully assembled, and the pivot screw is inserted and adjusted for optimal tension. Each pair undergoes rigorous quality checks, including testing on various materials, to ensure they meet our exacting standards before receiving the William Whiteley & Sons seal of approval.
08
Japanning the Handles
An old-fashioned term for painting, japanning is a process whereby each scissor handle is manually dipped first into primer, and then into paint. The scissors are left to drip dry, before the paint is then baked on in our oven. Not all our scissors have painted handles โ others may go for coating before assembly; this can range from chrome plating or golf plating, to Teflon coating or even titanium-nitride ceramic coating, which gives our gold EXOs their spectacular finish.
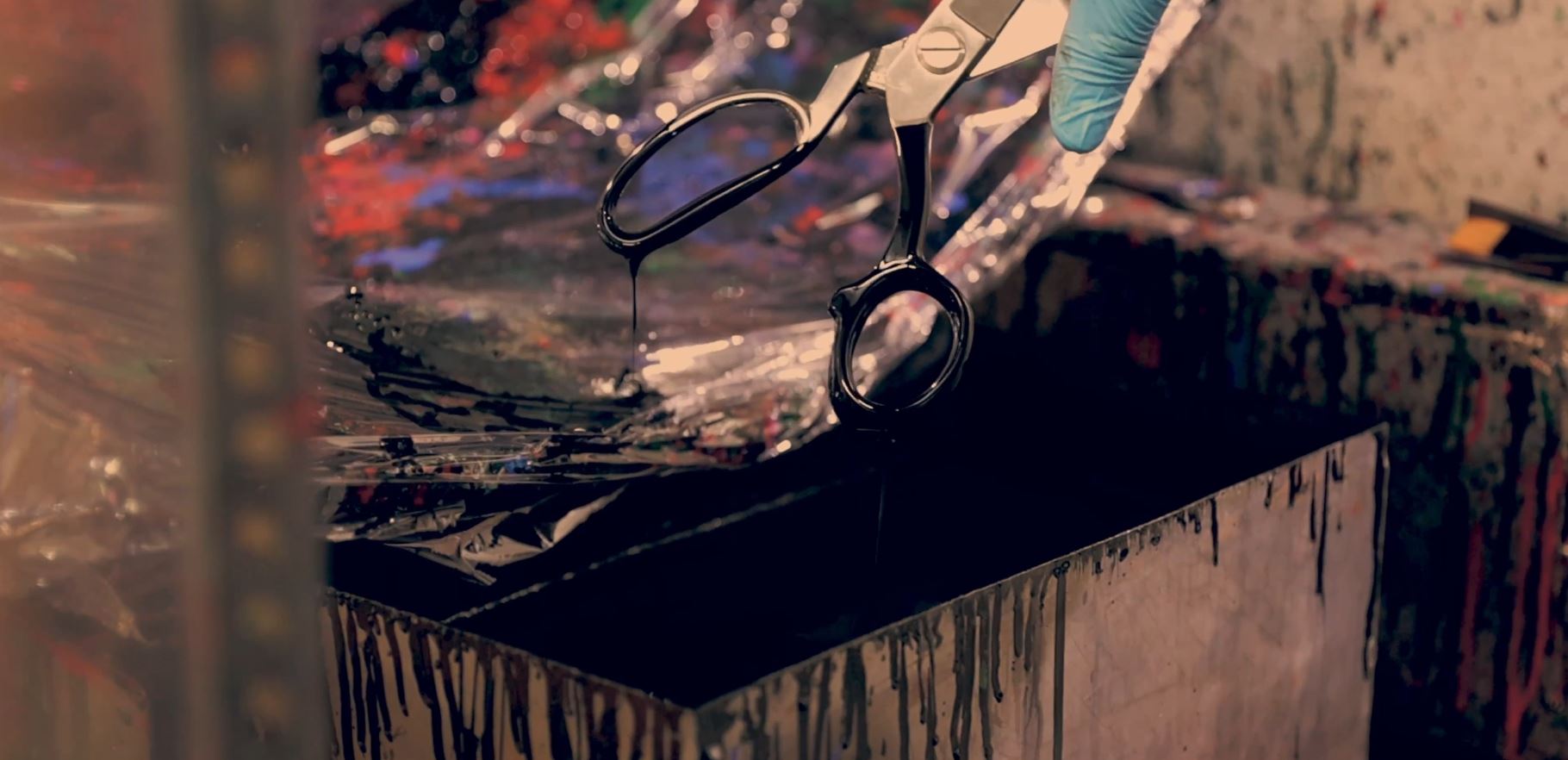
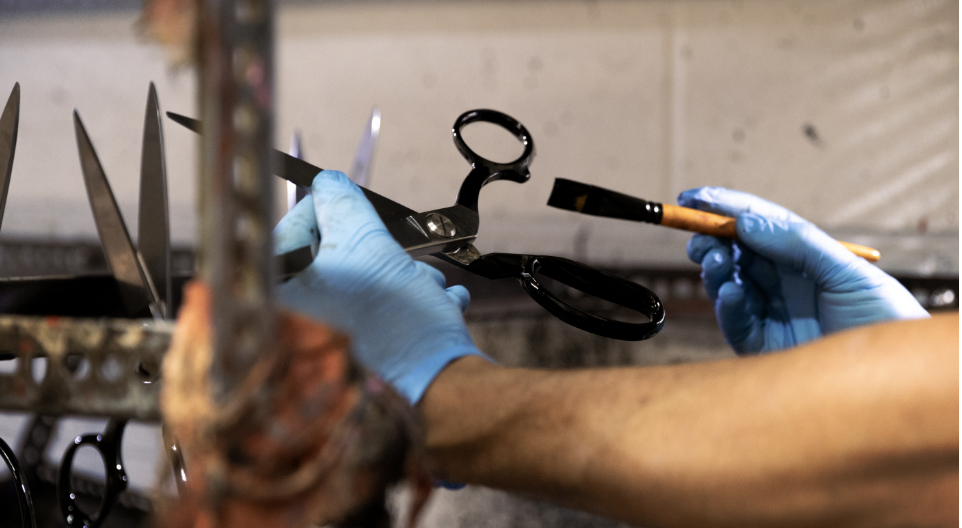
09
Personalisation & Shipping
The final stage in the process happens in our warehouse, where our scissors receive laser markings on the blades. Almost all our scissors have the option for personalisation, where a name, initials, company logo and more can be lasered onto the back blade.
Our warehouse team then sort, store, laser, label and ship each item around the world.